Drewno klejone: Co to jest? Zastosowanie, zalety 2025
Czy zastanawialiście się kiedyś, jak to możliwe, że konstrukcje drewniane osiągają tak imponujące rozpiętości i kształty, które jeszcze kilka dekad temu wydawałyby się czystą fantazją? Kluczem do tej inżynieryjnej magii jest drewno klejone. Ale czym dokładnie jest to drewno klejone? Mówiąc najprościej, to nowoczesny materiał budowlany, powstały poprzez łączenie wielu warstw drewna (lameli) w ściśle kontrolowanym procesie. Skrótowo, drewno klejone to wzmocniona, stabilniejsza i bardziej wszechstronna forma drewna, pozbawiona wielu wad naturalnego surowca, co otwiera przed budownictwem zupełnie nowe perspektywy.
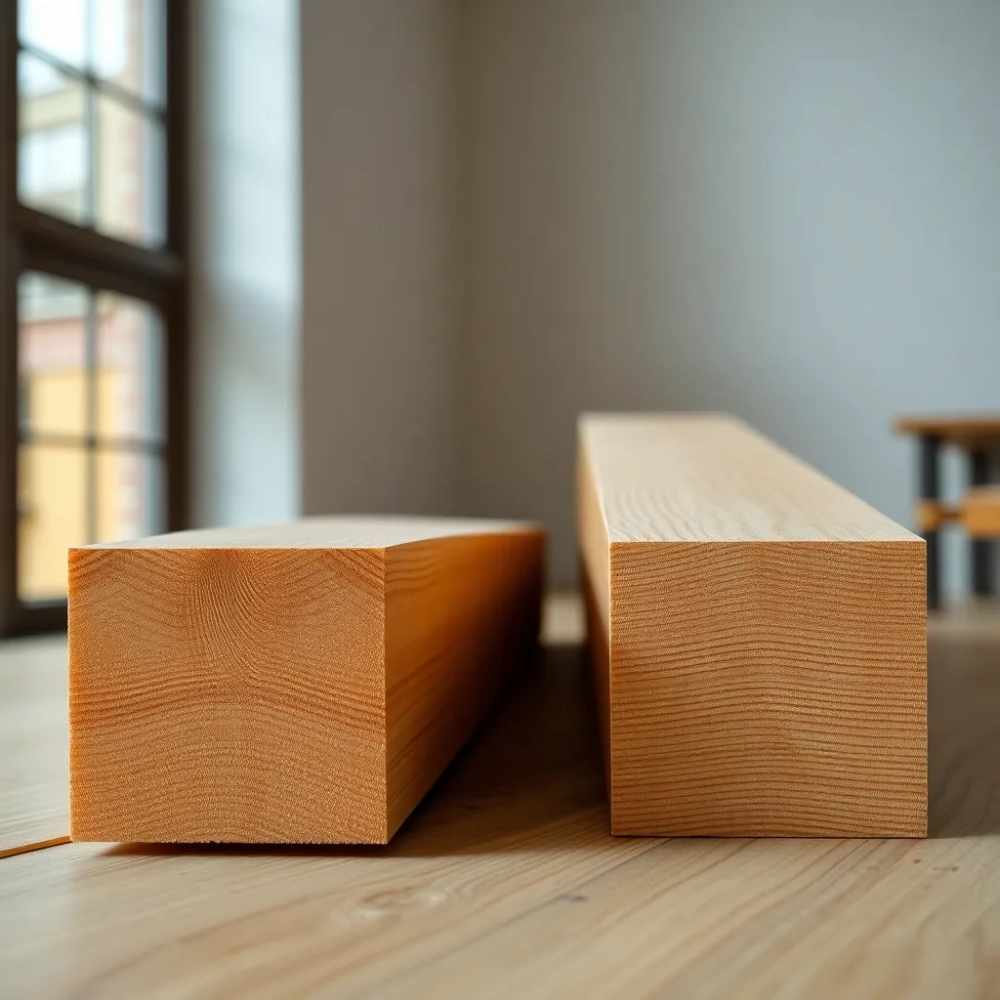
Zapewne każdy z nas spotkał się z nim, nieświadomie podziwiając majestatyczne konstrukcje dachów, innowacyjne mosty czy spektakularne obiekty sportowe. To materiał, który połączył w sobie ciepło i naturalność drewna z precyzją i wytrzymałością inżynierii. Co więcej, rozwój technologii klejenia oraz precyzyjnych metod obróbki sprawił, że możliwości zastosowania drewna klejonego stały się niemal nieograniczone, zrywając z tradycyjnym postrzeganiem drewna jako materiału o ograniczonych możliwościach konstrukcyjnych. Należy jednak pamiętać, że cała technologia wymaga bardzo ścisłego dopasowania poszczególnych parametrów produkcyjnych. Wygląda na to, że rynek drewna klejonego to przyszłość branży budowlanej.
Cecha/Parametr | Drewno lite | Drewno klejone | Jednostka/Komentarz |
---|---|---|---|
Wytrzymałość na zginanie | Średnia | Bardzo wysoka (nawet o 50-70% wyższa) | MPa, zależne od gatunku i klasy |
Stabilność wymiarowa | Niska (duże skurcze i pęcznienia) | Bardzo wysoka (minimalne odkształcenia) | Zminimalizowanie wypaczeń i pęknięć |
Odporność na wilgoć | Niska | Wysoka (dzięki selekcji drewna i klejom) | Impregnacja zwiększa odporność |
Rozpiętość konstrukcji | Ograniczona (maks. ~10-12m) | Duża (do 50 m i więcej) | Mosty, hale, dachy o dużych rozpiętościach |
Możliwość formowania | Bardzo ograniczona | Wysoka (krzywoliniowe elementy) | Elementy łukowe, kopuły |
Koszt materiału | Niższy | Wyższy (o ok. 20-40%) | Na etapie inwestycji |
Koszt montażu | Wyższy (wymaga wielu mniejszych elementów) | Niższy (duże, prefabrykowane elementy) | Oszczędność czasu i robocizny |
Drewno klejone to nie tylko materiał, to cała filozofia budownictwa, która stawia na innowacyjność, estetykę i trwałość. Dzięki niemu, z pozornie „prostego” surowca, jakim jest drewno, powstają konstrukcje o niebywałej wytrzymałości i niepowtarzalnym charakterze. Można by pomyśleć, że jest to materiał stworzony na miarę XXI wieku, doskonale odpowiadający na rosnące wymagania dotyczące zrównoważonego rozwoju i ekologii. Niejednokrotnie, na spotkaniach z architektami, widzę błysk w ich oku, gdy omawiamy możliwości, jakie daje drewno klejone warstwowo, szczególnie w kontekście skomplikowanych projektów o dużej rozpiętości.
Warto zwrócić uwagę, że popularność drewna klejonego to nie tylko wynik jego wytrzymałości, ale także estetyki. Elegancki wygląd naturalnego drewna, w połączeniu z możliwością tworzenia nieskończonych form, sprawia, że jest ono wyborem dla projektów, gdzie estetyka odgrywa równie ważną rolę, co funkcjonalność. Takie projekty to prawdziwa poezja budownictwa, która z każdym rokiem zyskuje coraz większe grono zwolenników. Powstaje pytanie, dlaczego akurat to rozwiązanie, w mojej opinii, jest coraz bardziej widoczne w całej branży. Głównie dlatego, że jest to naturalne i elastyczne rozwiązanie, co pozwala na różnorodność i budowanie z wizją na następne pokolenia.
Drewno klejone vs. Drewno lite – kluczowe różnice
Zawsze, gdy rozmawiam z klientami lub studentami architektury, pojawia się pytanie: skoro mamy tradycyjne, solidne drewno lite, to po co nam drewno klejone? To doskonałe pytanie, na które odpowiedź leży w fundamentalnych różnicach między tymi dwoma materiałami. Drewno lite, choć piękne i naturalne, ma swoje ograniczenia. Jest podatne na skurcze, pęcznienia, pęknięcia i odkształcenia, szczególnie przy dużych wymiarach i zmiennych warunkach wilgotnościowo-temperaturowych.
Wyobraźmy sobie tradycyjną belkę drewnianą. Kiedy słońce praży, a wilgotność spada, drewno kurczy się. Kiedy przychodzi deszczowa pogoda, pęcznieje. To naturalny proces, ale w konstrukcjach może prowadzić do niekontrolowanych ruchów, powstawania pęknięć i osłabienia całej konstrukcji. Znam przypadek, gdzie duża, lita belka dębowa, która miała być ozdobą salonu, po roku pękła wzdłuż, niszcząc cały efekt estetyczny i wprowadzając niemałe zamieszanie. To przykład, który dobrze obrazuje, dlaczego „lite” nie zawsze oznacza „lepsze”.
Natomiast drewno klejone warstwowo jest zupełnie inną bestią. Jest wytwarzane poprzez łączenie mniejszych lameli drewnianych, zazwyczaj o grubości od 20 do 45 mm, w większe elementy. Proces ten pozwala na eliminację wad naturalnego drewna, takich jak sęki czy pęknięcia, które osłabiają jego wytrzymałość. Dzięki odpowiedniemu ułożeniu słojów i zastosowaniu specjalistycznych klejów, materiał ten charakteryzuje się znacznie wyższą wytrzymałością na zginanie i ściskanie – nawet o 50-70% w porównaniu do drewna litego.
Kolejną kluczową różnicą jest stabilność wymiarowa. Klejenie wielu warstw drewna o przeciwstawnym układzie słojów lub poprzez staranne wysuszenie każdej lameli przed klejeniem minimalizuje ruchy drewna. Oznacza to, że elementy z drewna klejonego znacznie mniej kurczą się i pęcznieją pod wpływem zmian wilgotności i temperatury. Jeśli chcemy uniknąć problemów z wypaczaniem czy powstawaniem szczelin, klejone drewno jest tu niekwestionowanym zwycięzcą.
Jeśli chodzi o gabaryty i kształtowanie, drewno klejone jest bezkonkurencyjne. Drewno lite ma naturalne ograniczenia długości i przekroju, wynikające z wymiarów drzewa. Natomiast z klejonego drewna możemy tworzyć elementy o długościach przekraczających 50 metrów, a także dowolnie profilowane kształty – łuki, krzywe, fale. To otwiera zupełnie nowe możliwości projektowe, pozwalając architektom na realizację najbardziej śmiałych wizji, niemożliwych do osiągnięcia z użyciem drewna litego. Pamiętajmy, że budynek budujemy zazwyczaj raz w życiu, więc to rozwiązanie daje pełne pole do popisu, co nie jest w ogóle droższe, jeśli chodzi o realizację.
Odporność na ogień to kolejny aspekt, który często zaskakuje. Choć może się wydawać paradoksem, drewno klejone, ze względu na swój duży przekrój, charakteryzuje się przewidywalnym zachowaniem w pożarze. Powstaje na nim warstwa zwęglenia, która izoluje głębsze warstwy drewna, opóźniając jego spalenie. To sprawia, że konstrukcje z drewna klejonego mogą utrzymać swoją nośność dłużej niż konstrukcje stalowe w wysokiej temperaturze, które ulegają plastycznemu odkształceniu i tracą nośność znacznie szybciej.
Patrząc na cenę, początkowo drewno klejone może wydawać się droższe w zakupie niż drewno lite (średnio o 20-40% w przypadku standardowych belek). Jednakże, biorąc pod uwagę oszczędności na montażu (większe elementy, szybszy montaż) oraz znacznie dłuższą żywotność i mniejsze koszty utrzymania, inwestycja w drewno klejone często okazuje się bardziej opłacalna w dłuższej perspektywie. To jest ta różnica, którą trzeba wytłumaczyć klientom i to jest najważniejszy element, żeby wiedzieć, co klient naprawdę potrzebuje.
Podsumowując, choć drewno lite ma swój niezaprzeczalny urok i zastosowanie w wielu dziedzinach, drewno klejone wygrywa w konkurencji pod względem wytrzymałości, stabilności wymiarowej, możliwości konstrukcyjnych i efektywności w długim terminie. To materiał, który w rękach doświadczonego architekta i inżyniera staje się potężnym narzędziem do tworzenia innowacyjnych, trwałych i pięknych budowli. Nie jest to żadna fanaberia, to jest odpowiedź na wyzwania współczesnego budownictwa.
Zalety i właściwości drewna klejonego w budownictwie
Kiedy mówimy o drewnie klejonym w kontekście budownictwa, nie mówimy tylko o materiale, ale o kompleksowym rozwiązaniu, które przekłada się na konkretne korzyści dla inwestorów, wykonawców i przyszłych użytkowników obiektów. To trochę jak gra w szachy, gdzie każdy ruch musi być przemyślany. To rozwiązanie, które pozwala na uniknięcie wielu pułapek, typowych dla tradycyjnych metod budowlanych, zapewniając spokój i przewidywalność na każdym etapie projektu. Spokój zyskujemy, ponieważ to jest najlepszy materiał na rynku. Dzięki temu rozwiązaniu można spać spokojnie i nie zastanawiać się, czy aby na pewno nie będzie żadnych pęknięć.
Pierwszą i najważniejszą zaletą jest bezsprzecznie wytrzymałość i stabilność wymiarowa. Wyobraź sobie most czy dach o gigantycznej rozpiętości, który musi znieść potężne obciążenia – od ciężaru własnego, poprzez siłę wiatru, aż po nawis śniegu. Tradycyjne drewno lite nie sprostałoby takiemu wyzwaniu w tej skali, uległoby odkształceniom, pęknięciom, a w skrajnych przypadkach – katastrofie. Drewno klejone, dzięki specyfice produkcji (eliminacja wad, układ słojów, wysokiej jakości kleje), staje się super-materiałem. Z moich obserwacji, wytrzymałość na zginanie drewna klejonego jest dwukrotnie większa niż drewna litego, co pozwala na budowę smuklejszych, lżejszych, a jednocześnie bezpieczniejszych konstrukcji. To oznacza mniejsze obciążenia fundamentów i większą swobodę architektoniczną.
Kolejną, często niedocenianą zaletą, jest odporność na ogień. Tak, to nie pomyłka. Choć drewno jest materiałem palnym, grube przekroje drewna klejonego zachowują się w ogniu bardzo przewidywalnie. Podczas pożaru na powierzchni elementu tworzy się warstwa zwęglona, która działa jak izolacja, chroniąc wewnętrzne warstwy drewna przed dalszym paleniem. Oznacza to, że konstrukcja z drewna klejonego utrzymuje swoją nośność przez znacznie dłuższy czas niż np. stal, która w wysokiej temperaturze szybko traci swoje właściwości i ulega odkształceniom. Kiedyś byłem świadkiem symulacji pożarowej, gdzie stalowy element zapadł się po kilkunastu minutach, a belka z drewna klejonego po ponad godzinie nadal stała stabilnie. Robi to wrażenie, prawda?
Odporność na wilgoć i czynniki biologiczne to następny atut. Proces produkcyjny, który obejmuje suszenie drewna do odpowiedniej wilgotności (zazwyczaj 8-12%) i impregnację, eliminuje ryzyko rozwoju grzybów, pleśni i szkodników. Dzięki temu konstrukcje z drewna klejonego są trwalsze i mniej podatne na degradację w warunkach zmiennej wilgotności. To szczególnie ważne w przypadku obiektów narażonych na działanie warunków atmosferycznych, takich jak mosty, czy elementy fasad, ale również budynków o zwiększonej wilgotności wewnątrz, jak pływalnie czy hale sportowe. Pamiętam, jak jeden z naszych klientów, inwestujący w duży park wodny, początkowo wahał się przed użyciem drewna, obawiając się jego podatności na wilgoć. Kiedy jednak zrozumiał, że nowoczesne drewno klejone eliminuje ten problem, jego entuzjazm wzrósł niesamowicie.
Nie możemy zapomnieć o aspekcie ekologicznym i zrównoważonym rozwoju. Drewno jest materiałem odnawialnym, a produkcja drewna klejonego generuje znacznie niższy ślad węglowy niż produkcja stali czy betonu. Dodatkowo, dzięki precyzyjnemu wykorzystaniu surowca i minimalizacji odpadów, proces jest bardzo efektywny. W dobie rosnącej świadomości ekologicznej, wybór drewna klejonego to nie tylko decyzja ekonomiczna, ale także etyczna, wpisująca się w globalne trendy dbałości o środowisko naturalne. To przyszłość, do której każdy z nas powinien dążyć.
Estetyka i możliwości architektoniczne to cechy, które sprawiają, że drewno klejone jest ulubionym materiałem projektantów. Możliwość formowania elementów o niemal dowolnych kształtach – łukach, krzywiznach, falach – pozwala na realizację odważnych i unikalnych projektów. Co więcej, naturalny, ciepły wygląd drewna dodaje wnętrzom i fasadom elegancji i przytulności. Drewno klejone to nie tylko nośnik obciążeń, ale także integralny element estetyczny budynku, który wzbudza podziw i inspiruje. To dlatego wielu projektantów z pasją i zaangażowaniem wybiera to rozwiązanie.
Krótszy czas montażu i łatwość prefabrykacji to kolejny plus. Duże, precyzyjnie wykonane elementy z drewna klejonego są wytwarzane w fabryce, a następnie transportowane na plac budowy i montowane w ekspresowym tempie. To znacznie skraca czas budowy, redukuje koszty robocizny i minimalizuje ryzyko błędów. Przy dużych inwestycjach, gdzie czas to pieniądz, taka efektywność jest nie do przecenienia. Często słyszę od generalnych wykonawców, że wybór drewna klejonego na konstrukcję dachu pozwala zaoszczędzić tygodnie pracy w porównaniu z tradycyjnymi metodami, co jest kluczowe dla ich harmonogramu.
Reasumując, drewno klejone to nie tylko silny i stabilny materiał. To kompleksowe rozwiązanie, które oferuje wytrzymałość, bezpieczeństwo, odporność na czynniki zewnętrzne, ekologiczność, estetykę i efektywność budowy. To inwestycja, która zwraca się w postaci długotrwałej wartości, piękna i spokoju ducha. To trochę jak posiadanie „drewnianego superbohatera” w arsenale budowlanym, który jest w stanie sprostać nawet najtrudniejszym wyzwaniom.
Główne zastosowania drewna klejonego w konstrukcjach
Jeśli kiedykolwiek zastanawiałeś się, gdzie podziało się to ogromne drzewo, którego zdjęcie widziałeś w Internecie, to najprawdopodobniej zostało ono przetworzone w majestatyczną konstrukcję z drewna klejonego. To jest ten materiał, który w rękach architektów i inżynierów staje się prawdziwą „plasteliną” budownictwa, pozwalającą na tworzenie form, które jeszcze kilkadziesiąt lat temu byłyby trudne do wyobrażenia. Opowiem Wam, dlaczego drewno klejone zrewolucjonizowało budownictwo.
Przede wszystkim, drewno klejone jest królem wielkich rozpiętości. Mówimy tutaj o halach sportowych, basenach, centrach handlowych, a nawet lotniskach, gdzie potrzeba bezsłupowych przestrzeni. Wyobraźmy sobie konstrukcje dachowe, które bez podpór sięgają nawet 50 metrów – a w przypadku specjalnych, krzywoliniowych kształtów, nawet więcej! To właśnie dzięki wyjątkowej wytrzymałości i stabilności drewna klejonego możliwe jest budowanie takich imponujących obiektów, gdzie estetyka łączy się z funkcjonalnością. Bez tego materiału, takie projekty wymagałyby znacznie cięższych i droższych rozwiązań ze stali czy żelbetu.
Kolejnym obszarem, gdzie drewno klejone święci triumfy, są konstrukcje o nietypowych kształtach – łukowe, eliptyczne, faliste. Czy widzieliście kiedyś dach w kształcie odwróconego łuku lub falistej linii, która płynnie przechodzi z dachu w ścianę? To najczęściej zasługa drewna klejonego. Ze względu na swoją plastyczność w procesie produkcji, można mu nadać niemal dowolny kształt. Jest to szczególnie cenne w przypadku obiektów użyteczności publicznej, takich jak audytoria, kościoły, muzea czy pawilony wystawowe, gdzie estetyka i unikalny design odgrywają kluczową rolę. Znamy przypadek, gdzie do zaprojektowania dachu hali sportowej w Hiszpanii wykorzystano drewno klejone, dzięki czemu konstrukcja zyskała spektakularny, falujący kształt, idealnie komponujący się z otoczeniem. Niewiele innych materiałów dałoby taką swobodę.
Mosty i kładki to kolejne znaczące zastosowanie drewna klejonego. Dzięki swojej wytrzymałości, lekkości i odporności na czynniki zewnętrzne (zwłaszcza po odpowiedniej impregnacji), mosty drewniane klejone są coraz częściej wybierane jako alternatywa dla konstrukcji stalowych czy betonowych. Są lżejsze, co zmniejsza obciążenia na podłoże i fundamenty, a ich montaż jest znacznie szybszy. Dodatkowo, naturalny wygląd drewna pięknie komponuje się z krajobrazem, zwłaszcza w parkach, terenach zielonych czy historycznych obszarach. Pamiętam projekt kładki dla pieszych, gdzie zastosowanie drewna klejonego pozwoliło na zbudowanie elegnckiej, zakrzywionej konstrukcji o rozpiętości 25 metrów, która stała się atrakcją turystyczną w danej miejscowości.
W budownictwie mieszkaniowym drewno klejone znajduje zastosowanie głównie w formie belek stropowych, podciągów, a także jako elementy konstrukcyjne dachów, takie jak więźby dachowe i wiązary. Jego stabilność wymiarowa i nośność sprawiają, że można tworzyć większe i otwarte przestrzenie bez konieczności stosowania wielu podpór. W nowoczesnych domach szkieletowych oraz domach pasywnych i energooszczędnych drewno klejone jest często wybierane ze względu na swoje doskonałe właściwości izolacyjne oraz możliwość prefabrykacji ścian i dachów. To zdecydowanie przyspiesza proces budowy.
Prefabrykacja to zresztą osobna, bardzo ważna kategoria zastosowań. Fabryki drewna klejonego dostarczają na plac budowy gotowe elementy – belki, słupy, wiązary, a nawet całe moduły ścian i dachów – które są produkowane z najwyższą precyzją, zgodnie z projektem. To znacząco skraca czas budowy na miejscu, minimalizuje ilość odpadów i gwarantuje wysoką jakość wykonania. Widziałem, jak cały dach wielkopowierzchniowej hali był montowany w ciągu kilku dni, dzięki dostarczeniu prefabrykowanych elementów. Efektywność jest niesamowita.
Oprócz funkcji czysto konstrukcyjnych, drewno klejone ma również szerokie zastosowanie dekoracyjne. Ze względu na swój estetyczny wygląd i możliwość obróbki na gładką powierzchnię, jest często wykorzystywane do produkcji elementów widocznych we wnętrzach, takich jak belki stropowe, ramy okienne, drzwi, schody, meble czy nawet blaty kuchenne. Naturalne słoje drewna w połączeniu z precyzyjnym wykończeniem tworzą unikalne i ciepłe przestrzenie, które są bardzo cenione przez inwestorów. To również dobry sposób na wprowadzenie elementów natury do pomieszczeń, co coraz bardziej zyskuje na znaczeniu.
Warto również wspomnieć o zastosowaniu drewna klejonego w rolnictwie, gdzie buduje się z niego hale magazynowe, obory czy stajnie. W tym sektorze ceni się go za wytrzymałość, odporność na wilgoć oraz możliwość tworzenia dużych, otwartych przestrzeni, które są idealne do przechowywania maszyn rolniczych czy hodowli zwierząt. Jego właściwości fizykochemiczne sprawiają, że to najlepszy materiał do tworzenia trwałych i efektywnych konstrukcji.
Podsumowując, drewno klejone to prawdziwy materiał XXI wieku, który znajduje zastosowanie wszędzie tam, gdzie potrzebna jest wysoka wytrzymałość, stabilność wymiarowa, estetyka i możliwości tworzenia skomplikowanych form. Od majestatycznych dachów, przez eleganckie mosty, aż po precyzyjnie wykonane elementy wnętrz – to materiał, który zmienia oblicze współczesnego budownictwa i daje architektom niemal nieograniczone pole do popisu. Myślę, że jeszcze wiele nas zaskoczy w najbliższych latach.
Produkcja drewna klejonego – etapy i technologie
Zawsze, gdy widzę piękną, giętą belkę z drewna klejonego, zastanawiam się, ile pracy i precyzji włożono w jej stworzenie. To nie jest po prostu zlepianie desek. To skomplikowany, wieloetapowy proces technologiczny, który wymaga wiedzy, doświadczenia i specjalistycznych maszyn. Można powiedzieć, że produkcja drewna klejonego to taka alchemia, gdzie z prostych kawałków drewna tworzy się złoto budownictwa. Sam proces produkcji wygląda trochę jak tort warstwowy, ale z elementami inżynierii na najwyższym poziomie.
Wszystko zaczyna się od wyboru odpowiedniego surowca. To kluczowy etap. Nie każde drewno nadaje się do produkcji klejonego drewna. Zazwyczaj używa się drewna iglastego – świerka, sosny, modrzewia, sporadycznie dębu. Wybór drewna jest niezwykle selektywny: musi być wolne od poważnych wad, takich jak duże sęki, pęknięcia, czy oznaki chorób. Każda deska, zanim trafi na linię produkcyjną, jest skrupulatnie oceniana. To trochę jak casting do hollywoodzkiego filmu – tylko najlepsi przechodzą dalej. Niejednokrotnie na tym etapie selekcjonuje się drewno, którego usłojenie gwarantuje pożądaną wytrzymałość. Jest to najważniejszy element na samym początku produkcji.
Następnym etapem jest suszenie drewna. Jest to absolutnie krytyczny proces, bez którego nie ma mowy o produkcji wysokiej jakości drewna klejonego. Drewno jest suszone w specjalnych komorach suszarniczych do ściśle określonej wilgotności – zazwyczaj 8-12%. Dlaczego to takie ważne? Po pierwsze, eliminuje to ryzyko rozwoju grzybów, pleśni i larw owadów. Po drugie, stabilna wilgotność drewna jest niezbędna dla prawidłowego wiązania kleju i minimalizowania późniejszych odkształceń materiału. Wyobraźcie sobie klejenie dwóch mokrych desek – to tak, jakby próbować skleić lód – nic z tego nie wyjdzie trwałego. Suszenie to podstawa stabilności. W trakcie suszenia monitorowana jest temperatura, wilgotność oraz przepływ powietrza, by zapewnić równomierne odparowywanie wody.
Po wysuszeniu deski trafiają do strugania i optymalizacji. W tym procesie lamele są czterostronnie strugane, co zapewnia im gładką i jednolitą powierzchnię. To jest niezbędne dla precyzyjnego dopasowania i maksymalnej powierzchni styku, co jest kluczowe dla wytrzymałości spoiny klejowej. Jednocześnie na tym etapie następuje optymalizacja lameli – wszelkie mniejsze wady, które mogłyby osłabić konstrukcję, są wycinane, a zdrowe kawałki drewna łączone na mikrowczepy. Takie połączenia, choć wydają się maleńkie, są niezwykle mocne i pozwalają na uzyskanie lameli o praktycznie nieograniczonej długości. Mikrowczepy to prawdziwy game changer w branży.
Kolejny krok to sortowanie lameli. Deski po obróbce są sortowane pod kątem wytrzymałości. Dzięki temu możliwe jest układanie w poszczególnych warstwach elementu klejonego drewna lameli o różnych klasach wytrzymałości – mocniejsze lamele na zewnątrz (gdzie naprężenia są największe) i słabsze w środku. Taka optymalizacja pozwala na uzyskanie maksymalnej wytrzymałości przy optymalnym zużyciu surowca, a także wpływa na koszt końcowy produktu.
Sercem procesu jest klejenie. W zależności od wielkości elementu i zastosowania, stosuje się różne rodzaje klejów (np. melaminowo-moczniki, poliuretanowe). Klej jest nanoszony na powierzchnię lameli, a następnie deski są układane jedna na drugiej. W małych warsztatach stolarskich odbywa się to ręcznie, a lamele są unieruchamiane za pomocą ścisków. W dużych fabrykach proces jest w pełni zautomatyzowany. Lamele trafiają do specjalistycznych pras – hydraulicznym lub próżniowych. To właśnie prasy zapewniają odpowiedni nacisk, który jest kluczowy dla właściwego wiązania kleju. Ten proces trwa od kilku do kilkunastu godzin, w zależności od rodzaju kleju i wymiarów elementu.
Po zakończeniu prasowania, następuje końcowa obróbka i wykończenie. Elementy z drewna klejonego są docinane na wymiar, frezowane, a ich powierzchnia jest dodatkowo szlifowana. W tym etapie możliwe jest również nadanie belkom nietypowych kształtów, np. łukowych. Niektóre elementy poddawane są również impregnacji ciśnieniowej lub zanurzeniowej, co zwiększa ich odporność na czynniki zewnętrzne. Kontrola jakości na tym etapie jest niezwykle rygorystyczna, aby gotowy produkt spełniał wszystkie normy i oczekiwania klienta.
Współczesne fabryki drewna klejonego to imponujące kompleksy, gdzie roboty współpracują z maszynami sterowanymi numerycznie (CNC), co gwarantuje precyzję, szybkość i powtarzalność. Możliwe jest również produkowanie elementów na specjalne zamówienie, zgodnie z indywidualnymi wytycznymi projektanta danej konstrukcji – od miniaturowych belki po gigantyczne łuki o rozpiętości kilkudziesięciu metrów. Widziałem, jak z pojedynczych lameli powstają potężne belki, które po złożeniu w całość stworzyły dach imponującego centrum sportowego. To było jak obserwowanie magii w działaniu!
Proces produkcji drewna klejonego to dowód na to, jak nowoczesne technologie potrafią w pełni wykorzystać potencjał naturalnego surowca, eliminując jego wady i potęgując zalety. To nie jest po prostu zlepianie, to precyzyjna inżynieria, która dostarcza budownictwu materiał przyszłości. Dzięki temu procesowi uzyskujemy materiał, który łączy w sobie naturę i najnowsze zdobycze techniki, otwierając drzwi do nieskończonych możliwości w projektowaniu i budowaniu. To jest ten materiał, którego z pewnością będziemy widzieć coraz więcej w przestrzeni publicznej.
Najczęściej zadawane pytania o drewno klejone
1. Czym jest drewno klejone i czym różni się od drewna litego?
Drewno klejone to materiał konstrukcyjny powstały przez sklejenie wielu warstw cieńszych desek (lameli). Główna różnica polega na eliminacji wad drewna litego (sęki, pęknięcia), co przekłada się na znacznie wyższą wytrzymałość, stabilność wymiarową oraz możliwość tworzenia elementów o dużych gabarytach i nietypowych kształtach, niemożliwych do uzyskania z litego drewna.
2. Czy drewno klejone jest odporne na wilgoć i ogień?
Tak, drewno klejone charakteryzuje się wysoką odpornością na wilgoć, dzięki procesowi suszenia drewna przed klejeniem i zastosowaniu odpowiednich klejów. Co do ognia, mimo że drewno jest materiałem palnym, grube przekroje drewna klejonego tworzą zwęgloną warstwę izolacyjną, która spowalnia spalanie i pozwala konstrukcji zachować nośność dłużej niż np. konstrukcje stalowe w wysokiej temperaturze.
3. Gdzie najczęściej stosuje się drewno klejone w budownictwie?
Drewno klejone znajduje szerokie zastosowanie w konstrukcjach o dużych rozpiętościach, takich jak hale sportowe, baseny, mosty, a także w obiektach wymagających nietypowych kształtów (np. łukowych dachów). Wykorzystuje się je również w budownictwie mieszkaniowym jako belki stropowe, więźby dachowe oraz w elementach ozdobnych wnętrz, dzięki jego estetycznemu wyglądowi.
4. Jakie są etapy produkcji drewna klejonego?
Proces produkcji obejmuje: wybór i selekcję surowca drzewnego, suszenie lameli do odpowiedniej wilgotności, struganie i optymalizację (usuwanie wad, łączenie na mikrowczepy), sortowanie pod kątem wytrzymałości, a następnie klejenie w prasach pod ciśnieniem. Ostatnim etapem jest końcowa obróbka, czyli docinanie, szlifowanie i ewentualna impregnacja gotowych elementów.
5. Czy drewno klejone jest droższe od drewna litego?
Początkowy koszt zakupu drewna klejonego może być wyższy niż drewna litego. Jednak w dłuższej perspektywie, biorąc pod uwagę oszczędności na szybszym montażu, dłuższą żywotność konstrukcji, mniejsze wymagania konserwacyjne oraz wyższą wytrzymałość i stabilność wymiarową, inwestycja w drewno klejone często okazuje się bardziej opłacalna i efektywna kosztowo.