Jaka wełna pod elewację drewnianą? Poradnik 2025
Marzysz o elewacji drewnianej, która nada Twojemu domowi niepowtarzalny charakter? To świetna decyzja! Drewno to materiał ponadczasowy, ciepły i ekologiczny. Ale czy zastanawiałeś się, jaka wełna pod elewację drewnianą będzie optymalnym wyborem, aby piękno szło w parze z funkcjonalnością? W skrócie, wełna mineralna (skalna lub szklana) jest najczęściej rekomendowanym materiałem izolacyjnym pod elewacje drewniane, ze względu na swoją trwałość i niepalność. Jednakże, nie jest to jedyne rozwiązanie, które zasługuje na uwagę – rynek oferuje szereg innych, ciekawych opcji, które mogą Cię zaskoczyć. Dziś zanurkujemy w świat izolacji, byś podjął świadomą decyzję, która zapewni Twojemu domowi nie tylko estetyczny wygląd, ale i lata komfortu.
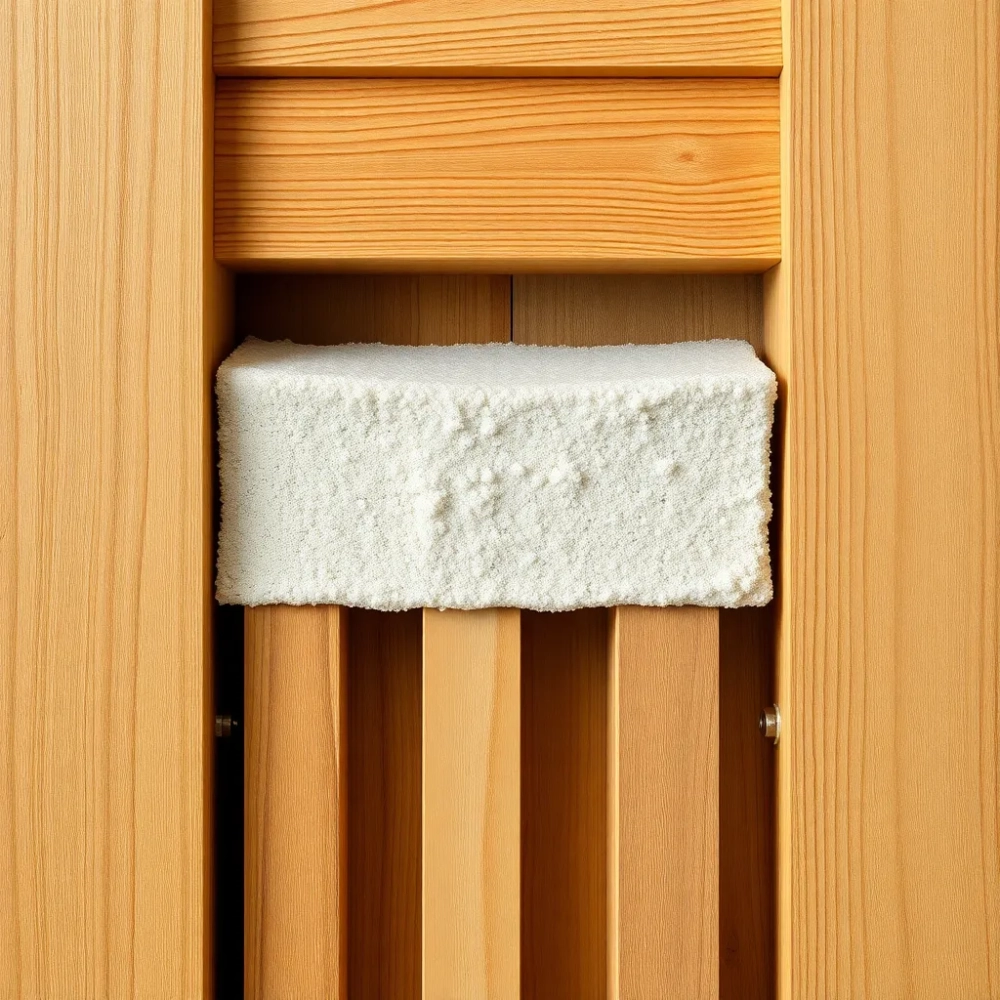
Wybór odpowiedniej izolacji to klucz do energooszczędności i komfortu mieszkania. Przyjrzyjmy się, jak różne materiały radzą sobie w praktyce. Dane te mogą stanowić punkt wyjścia do głębszej analizy, ale pamiętaj, że warunki lokalne i specyfika projektu zawsze będą miały decydujący wpływ na ostateczny wybór.
Materiał Izolacyjny | Współczynnik Lambda (W/mK) | Gęstość (kg/m³) | Orientacyjna Cena (PLN/m² dla 15 cm) | Główne Zalety |
---|---|---|---|---|
Wełna Mineralna (skalna) | 0.035 - 0.040 | 30 - 150 | 40 - 70 | Niepalność, paroprzepuszczalność, dobra izolacja akustyczna |
Wełna Mineralna (szklana) | 0.032 - 0.040 | 10 - 30 | 30 - 60 | Niska waga, elastyczność, dobra izolacja akustyczna |
Wełna Drzewna | 0.038 - 0.045 | 110 - 200 | 80 - 120 | Ekologiczna, wysoka pojemność cieplna, regulacja wilgotności |
Wełna Konopna | 0.040 - 0.045 | 30 - 50 | 90 - 130 | Naturalna, paroprzepuszczalna, odporna na pleśń |
Tabela jasno pokazuje, że każdy z wymienionych materiałów ma swoje mocne strony, ale różnice w cenie i właściwościach termicznych są zauważalne. Kwestia wyboru odpowiedniej izolacji to złożony problem, który wymaga uwzględnienia wielu czynników, od lokalnych warunków klimatycznych po indywidualne preferencje estetyczne i budżetowe. Warto również pamiętać, że samo wybranie materiału to dopiero początek drogi. Równie ważne jest prawidłowe wykonanie montażu, co obejmuje odpowiednią grubość warstwy izolacyjnej, precyzyjne dopasowanie płyt oraz zastosowanie właściwego rusztu i kołkowania, które zapewnią stabilność i trwałość całej konstrukcji. Zanim podejmiesz ostateczną decyzję, warto skonsultować się ze specjalistami, którzy pomogą Ci dopasować rozwiązanie idealne do Twoich potrzeb i specyfiki budynku.
Wełna drzewna i konopna – alternatywy dla elewacji drewnianej
Choć wełna mineralna niezmiennie króluje na budowach, to świat budownictwa dynamicznie ewoluuje w kierunku rozwiązań bardziej ekologicznych i odnawialnych. Kiedy rozważasz jaka wełna pod elewację drewnianą będzie najlepsza, warto przyjrzeć się wełnie drzewnej i konopnej – prawdziwym "zielonym" alternatywom, które oferują unikalne korzyści. Te materiały nie tylko efektywnie izolują, ale także doskonale wpisują się w trend zrównoważonego budownictwa, minimalizując nasz ślad węglowy. Wybór należy do Ciebie, ale my przedstawiamy fakty.
Wełna drzewna, jak sama nazwa wskazuje, produkowana jest z włókien drzewnych. Charakteryzuje się nie tylko bardzo dobrym współczynnikiem izolacji termicznej (często porównywalnym z wełną mineralną, rzędu 0.038-0.045 W/mK), ale również zdolnością do akumulowania ciepła. Oznacza to, że materiał ten doskonale sprawdza się w przypadku letnich upałów, zapobiegając przegrzewaniu się pomieszczeń, a zimą stabilizuje temperaturę. W kontekście izolacji elewacji drewnianej, ta właściwość jest niezwykle cenna. Przy zakupie, spodziewaj się cen w przedziale 80-120 PLN za metr kwadratowy dla grubości 15 cm, co czyni ją nieco droższą opcją.
Wełna konopna to kolejna propozycja z "zielonego" worka, która zyskuje na popularności. Wytwarzana z naturalnych włókien konopi siewnych, jest materiałem w pełni odnawialnym i biodegradowalnym. Jej parametry termiczne są zbliżone do wełny drzewnej (około 0.040-0.045 W/mK), ale to jej odporność na pleśnie i szkodniki oraz doskonała paroprzepuszczalność często decydują o wyborze. Wyobraź sobie ściany, które "oddychają" – to właśnie wełna konopna potrafi zapewnić. W przypadku cen, konopie plasują się nieco powyżej wełny drzewnej, z cenami od 90 do 130 PLN za metr kwadratowy (dla grubości 15 cm). Montaż wełny drzewnej i konopnej przypomina układanie wełny mineralnej – płyty wciska się między elementy rusztu i ewentualnie kołkuje.
Jednakże, pomimo swoich niewątpliwych zalet, te materiały mają też swoje wyzwania. Zwykle są droższe niż ich mineralne odpowiedniki. Może być to czynnik decydujący dla wielu inwestorów. Co więcej, dostępność na rynku wciąż bywa mniejsza, co może wpływać na terminy dostaw i zakres wyboru producentów. Z perspektywy redakcji, zawsze zachęcamy do rozważenia wszystkich za i przeciw, aby finalna decyzja była najbardziej świadoma. Pamiętaj, że inwestycja w dom to inwestycja na lata, a wybór izolacji to nie miejsce na kompromisy, które mogą negatywnie wpłynąć na komfort życia i koszty eksploatacji.
Grubość izolacji i montaż wełny pod deskami elewacyjnymi
Kwestia odpowiedniej grubości izolacji to fundament efektywności energetycznej Twojego domu i kluczowa decyzja, gdy zastanawiasz się, jaka wełna pod elewację drewnianą będzie najlepsza. Wcale nie jest to prosta odpowiedź „im więcej, tym lepiej”. Jest to skomplikowana gra zmiennych, obejmująca strefę klimatyczną, typ konstrukcji ściany, a nawet materiał, z którego zbudowany jest budynek. Na tym etapie, samodzielne podejmowanie decyzji może okazać się błędem. Zalecamy z całego serca, aby powierzyć kwestię doboru grubości warstwy termoizolacyjnej specjalistom – doświadczonemu projektantowi, wykwalifikowanemu szefowi firmy budowlanej lub audytorowi energetycznemu. To oni, bazując na aktualnych przepisach i normach (takich jak Warunki Techniczne WT 2021 w Polsce, które określają maksymalne wartości współczynnika przenikania ciepła U dla przegród), pomogą Ci osiągnąć optymalne parametry. Zazwyczaj dla standardowej grubości izolacji pod elewację drewnianą, stosuje się wełnę o grubości od 15 do 25 cm, układaną w systemie dwuwarstwowym.
Przejdźmy do sedna – montażu. Bez względu na to, czy wybierzesz wełnę mineralną, drzewną czy konopną, zasady są podobne. Wełniane płyty lub maty układa się między elementami rusztu, o którym szerzej opowiemy w kolejnym rozdziale. Najczęściej stosuje się metodę dwuwarstwową: pierwszą warstwę wkłada się na "wcisk" pomiędzy pionowe elementy rusztu. Następnie, na wierzch układa się drugą warstwę, prostopadle do pierwszej, co skutecznie eliminuje mostki termiczne i zapewnia ciągłość izolacji. Ten "wcisk" jest kluczowy, by uniknąć jakichkolwiek szczelin, przez które mogłoby uciekać ciepło. Pamiętaj, że nawet niewielka szczelina może obniżyć efektywność całej izolacji o kilkanaście procent.
Po ułożeniu wełny niezwykle istotne jest zabezpieczenie jej przed wilgocią z zewnątrz oraz wiatrem. Służy do tego specjalna membrana wiatroizolacyjna (często nazywana folią wiatroizolacyjną). Jest ona paroprzepuszczalna, co oznacza, że pozwala na odprowadzanie wilgoci z wnętrza ściany na zewnątrz, jednocześnie chroniąc izolację przed nawiewaniem zimnego powietrza. Membranę mocuje się do rusztu za pomocą zszywek, z zakładami, aby zapewnić ciągłość i szczelność. Orientacyjnie, metr kwadratowy dobrej jakości membrany kosztuje od 4 do 8 PLN, w zależności od jej parametrów.
Prawidłowe wykonanie montażu izolacji jest równie ważne jak sam wybór materiału. Zaniedbania na tym etapie mogą skutkować nie tylko utratą ciepła, ale także zawilgoceniem izolacji i degradacją konstrukcji. Znam historię klienta, który zaoszczędził na fachowcach, licząc, że "każdy umie ułożyć wełnę". Po kilku latach budynek zaczął pokazywać pierwsze symptomy problemów: grzyb w narożnikach, podwyższone rachunki za ogrzewanie. Okazało się, że izolacja była ułożona chaotycznie, pełna szczelin i mostków termicznych. Remont był kosztowny i czasochłonny. Takie studium przypadku dobitnie pokazuje, że warto zainwestować w sprawdzoną ekipę, która posiada doświadczenie w montażu wełny pod elewację drewnianą.
Ruszt pod elewację drewnianą: rodzaje i montaż izolacji
Kiedy planujemy, jaka wełna pod elewację drewnianą ma zostać zastosowana, nie możemy zapominać o fundamencie, na którym wszystko się opiera – ruszcie. To nie jest po prostu konstrukcja, która "jakoś" podtrzymuje deski elewacyjne. Ruszt to szkielet, który nie tylko zapewnia wsparcie dla okładziny, ale także odgrywa kluczową rolę w wentylacji i prawidłowym funkcjonowaniu całej elewacji. Jest to serce systemu, które umożliwia "oddychanie" ściany, a także chroni izolację przed niepożądanymi czynnikami zewnętrznymi.
Najczęściej spotykanym typem rusztu jest ten wykonany z drewna. W tym przypadku, kluczowe są wymiary i odpowiednie przygotowanie materiału. Belki o wymiarach 4 cm x 6 cm lub 4 cm x 12 cm (w zależności od wymaganej grubości izolacji) powinny być struganych i obowiązkowo zaimpregnowane ciśnieniowo lub suszone komorowo. Takie przygotowanie drewna gwarantuje jego trwałość i odporność na wilgoć, grzyby oraz szkodniki. Odstępy między pionowymi belkami rusztu powinny wynosić nie więcej niż 60 cm, aby zapewnić stabilne podparcie dla płyt izolacyjnych i desek elewacyjnych. Dobrze jest mierzyć rozstaw tak, aby dopasować go do szerokości płyt wełny, co minimalizuje ilość odpadów i przyspiesza montaż.
Montaż rusztu do ściany jest kluczowy dla uniknięcia mostków termicznych. Belki mocuje się do podłoża za pomocą specjalnych kotew lub kątowników, które pozwalają na odsunięcie drewna od powierzchni ściany o 5-10 cm. Ta przestrzeń umożliwia umieszczenie pierwszej warstwy wełny izolacyjnej, co eliminuje bezpośredni kontakt drewna ze ścianą i zapobiega utracie ciepła. Wyobraź sobie most termiczny jak otwarte okno, przez które ucieka ciepło – dzięki tej technice zamykamy je na cztery spusty.
Po ułożeniu izolacji i zamocowaniu membrany wiatroizolacyjnej, do belek rusztu przybija się listwy dystansowe. Te niewielkie, ale niezwykle ważne elementy (zwykle o grubości 2-3 cm) zapewniają przestrzeń wentylacyjną między okładziną elewacyjną a membraną wiatroizolacyjną. Minimalny odstęp to 30 mm, choć specjaliści często zalecają większy, zwłaszcza w przypadku wyższych budynków. Ta szczelina jest niezbędna do prawidłowej cyrkulacji powietrza, co odprowadza wilgoć z konstrukcji, zapobiega rozwojowi pleśni i przedłuża żywotność elewacji. Deski elewacyjne mocuje się do tych listew. Jeżeli marzy Ci się elewacja z deskami ułożonymi pionowo, potrzebujesz dodatkowego rzędu listew prostopadłych do pierwszych. To dodaje pracy, ale efekt jest często spektakularny.
Oprócz rusztu drewnianego, istnieją również rozwiązania z innych materiałów. Coraz częściej na rynku dostępne są systemy oparte na elementach stalowych lub aluminiowych. Są one droższe, ale oferują większą stabilność wymiarową i odporność na czynniki zewnętrzne. Aluminiowe profile są lekkie i odporne na korozję, co sprawia, że są idealne do zastosowania w trudnych warunkach. Niezależnie od wybranego materiału, prawidłowe wykonanie rusztu to gwarancja długotrwałej i bezproblemowej eksploatacji elewacji drewnianej.
Kołkowanie wełny – dlaczego jest tak ważne dla trwałości izolacji?
Kiedy stoisz przed wyzwaniem ocieplenia budynku i zastanawiasz się, jaka wełna pod elewację drewnianą będzie idealna, kwestia kołkowania wydaje się być technicznym detalem. Jednak pozory mylą! To właśnie te niepozorne elementy odgrywają kluczową rolę w zapewnieniu stabilności i długowieczności całej izolacji. Czy kołkowanie jest zawsze konieczne? Powiedzmy sobie szczerze: często słyszymy „nie zawsze”, ale tak naprawdę zawsze lepiej to zrobić. Lepiej zabezpieczyć płyty izolacyjne przed osiadaniem i potencjalnymi problemami, niż później borykać się z konsekwencjami. Traktuj to jako inwestycję w spokój ducha i trwałość konstrukcji. W końcu nikt nie chce widzieć, jak po kilku latach izolacja zaczyna się osuwać, prawda?
Kołkowanie to proces mechanicznego mocowania płyt izolacyjnych do ściany nośnej. Technicznie rzecz biorąc, aby prawidłowo przytwierdzić płytę, należy najpierw wywiercić w niej otwór o średnicy dopasowanej do średnicy kołka, który sięga mniej więcej 4 cm w głąb podłoża. Po umieszczeniu kołka, należy go dokręcić (w przypadku kołków rozporowych) lub wbić (w przypadku kołków wbijanych, szczególnie polecanych do podłoży z litego drewna lub betonu). Kołki powinny być rozmieszczone równomiernie, w liczbie mniej więcej 4 sztuk na 1 metr kwadratowy powierzchni. To minimum, które zazwyczaj wystarcza, aby stabilnie utrzymać wełnę na miejscu. W miejscach narożnych lub wokół otworów okiennych i drzwiowych, gdzie obciążenia są większe, często zwiększa się liczbę kołków do 6-8 sztuk na metr kwadratowy. Pamiętaj, że każdy producent wełny mineralnej ma również swoje zalecenia, które należy uwzględnić.
Rola kołkowania jest wieloraka. Po pierwsze, zapobiega osiadaniu się wełny, które mogłoby prowadzić do powstania szczelin i mostków termicznych. Zjawisko to jest szczególnie groźne w przypadku ciężkich płyt wełny skalnej, choć wełna szklana również z czasem może ulec nieznacznemu osiadaniu. Po drugie, kołki doskonale dociskają każdą płytę do ściany, eliminując wszelkie niedokładności montażowe i zapewniając idealne przyleganie izolacji. To klucz do zapewnienia ciągłości warstwy termicznej. Po trzecie, kołkowanie stanowi dodatkowe zabezpieczenie przed silnymi podmuchami wiatru, które w przypadku elewacji wentylowanych mogą wytworzyć siły ssące, potencjalnie odrywające izolację od ściany. Mam w pamięci przypadek pewnego budynku na wybrzeżu, gdzie zrezygnowano z kołkowania, myśląc, że „ruszt wystarczy”. Pierwszy silniejszy sztorm rozwiał płyty izolacyjne po okolicy niczym pierze. Lekcja? Nie oszczędzaj na kołkach.
Warto dopilnować, aby kołki były wykonane z materiałów odpornych na korozję, zwłaszcza ich trzpienie, jeśli stykają się z wilgotnym powietrzem wewnątrz ściany. Na rynku dostępne są kołki z trzpieniem plastikowym lub stalowym ocynkowanym, często z główką z tworzywa sztucznego, która minimalizuje mostki termiczne. Pamiętaj, że odpowiedni dobór długości kołków jest kluczowy – muszą one wystarczająco głęboko zakotwić się w ścianie nośnej. Zbyt krótkie kołki mogą po prostu nie spełnić swojego zadania. Kołkowanie to mały koszt w ogólnym budżecie projektu, ale jego brak może generować ogromne straty w przyszłości. Nie ma co igrać z grawitacją i siłami natury; odpowiednio zakotwiona wełna to gwarancja spokoju i ciepła w Twoim domu przez lata.
Q&A
Jaka wełna pod elewację drewnianą jest najlepsza pod kątem ognioodporności?
Pod kątem ognioodporności najlepsza jest wełna mineralna, zwłaszcza skalna, która jest materiałem niepalnym i charakteryzuje się wysoką temperaturą topnienia, co znacznie zwiększa bezpieczeństwo pożarowe budynku.
Czy wełna drzewna i konopna mogą zastąpić wełnę mineralną pod elewacją drewnianą?
Tak, wełna drzewna i wełna konopna stanowią ekologiczne i skuteczne alternatywy dla wełny mineralnej. Oferują one dobre parametry izolacyjne, wysoką pojemność cieplną oraz są paroprzepuszczalne, co sprzyja zdrowemu mikroklimatowi w domu. Wybór zależy od indywidualnych preferencji i budżetu.
Jakiej grubości izolacji użyć pod elewację drewnianą?
Optymalna grubość izolacji pod elewację drewnianą najczęściej waha się od 15 do 25 cm. Dokładną grubość należy określić na podstawie projektu budowlanego, uwzględniając obowiązujące normy i przepisy dotyczące współczynnika przenikania ciepła U, a najlepiej skonsultować się z fachowcem – projektantem lub audytorem energetycznym.
Jak ważne jest kołkowanie wełny pod elewacją drewnianą?
Kołkowanie jest niezwykle ważne dla trwałości i stabilności izolacji. Zapobiega osiadaniu się wełny, zapewnia jej prawidłowe przyleganie do ściany oraz chroni przed działaniem silnych wiatrów. Zaleca się stosowanie około 4 kołków na metr kwadratowy powierzchni izolacji.
Czym charakteryzuje się ruszt pod elewację drewnianą?
Ruszt pod elewację drewnianą to konstrukcja (najczęściej drewniana, struganych i impregnowana, lub rzadziej stalowa/aluminiowa), mocowana do ściany za pomocą kotew, która tworzy przestrzeń dla izolacji i zapewnia wentylację elewacji. Kluczowe są odpowiednie wymiary belek (np. 4x6 cm), rozstaw (do 60 cm) i zastosowanie listew dystansowych tworzących szczelinę wentylacyjną (min. 30 mm).